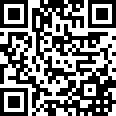
Mr. Liu Bin
Leave a messageMr. Liu Bin
Leave a message1. Need to polish in the early stage
However, the galvanized layer of the weld must be polished away, otherwise bubbles, trachoma, and false welding will occur. It also makes the weld brittle and the rigidity decreases.
2. the welding characteristics of galvanized steel
Galvanized steel is generally coated with a layer of zinc outside the low carbon steel, and the galvanized layer is generally 20 um thick. Zinc has a melting point of 419 ° C and a boiling point of about 908 ° C. In welding, zinc melts into a liquid that floats on the surface of the bath or at the root of the weld. Zinc has a large solid solubility in iron, zinc liquid will deeply etch the weld metal along the grain boundary, and low melting point zinc forms "liquid metal embrittlement".
At the same time, zinc and iron can form intermetallic brittle compounds, and these brittle phases reduce the plasticity of the weld metal and cause cracks under tensile stress.
If weld fillet welds, especially fillet welds of T-joints, are most susceptible to penetration cracks. When the galvanized steel is welded, the zinc layer on the surface and the edge of the groove is oxidized, melted and evaporated under the action of arc heat to volatilize white smoke and steam, which easily causes weld pores.
3. Welding process control
The pre-weld preparation of galvanized steel is the same as that of ordinary low-carbon steel. It is necessary to pay attention to the groove size and the nearby galvanized layer. For the penetration, the groove size should be appropriate, generally 60~65°, to leave a certain gap, generally 1.5~2.5mm; in order to reduce the penetration of zinc into the weld, the galvanized inside the groove can be welded before welding After the layer is removed, it is soldered again.
Welding method: When welding the first layer of welds of multi-layer welding, the zinc layer is melted as much as possible and vaporized and evaporated to escape the weld seam, which can greatly reduce the liquid zinc remaining in the weld.
When welding the fillet weld, the zinc layer is also melted as much as possible in the first layer and vaporized and evaporated to escape the weld. The method is to first move the end of the electrode forward about 5~7 mm, when the zinc layer is made. After melting, return to the original position and continue to weld forward.
In the case of cross-welding and vertical welding, if short-slag welding rods such as J427 are used, the tendency of undercutting will be small; if the round-trip transportation technology is used, the quality of non-defective welding can be obtained.